North-west Queensland is remote country, home to scattered towns such as Mount Isa, Cloncurry and Hughenden. It’s a place where distances are measured in hours it takes to drive rather than kilometres.
Across the region are businesses where machinery, parts and stock must be delivered in a timely manner. If you’re waiting a week for parts to arrive, staff aren’t working and money is being lost hand over fist.
RUSH JOB
When operating hundreds of kilometres away from the nearest supply hub, planning is everything—but sometimes, even the best-prepared teams need a rapid fix.
That was the case for Guerrilla Maintenance Services (GMS), an Indigenous-owned and operated maintenance, construction, and engineering company based in Cloncurry, Queensland. While running a brownfield project near Tennant Creek in the Northern Territory, GMS suddenly found itself in need of a critical component to keep the job on track.
GMS operations manager Clint Turner picked up the phone and called CSS member Mount Isa Mining Supplies. The part was in stock, but it was 660km away. “Clint wanted to know if we could get it to him that day,” recalls Brett Peterson, founder and manager of Mount Isa Mining Supplies. “No problem. We put it in the back of a ute and drove it to Tennant Creek. One of our staff members added a 13-hour round trip drive to his workday but the component was delivered on time.”
OVERCOMING REMOTE
GMS is no stranger to the demands of remote projects. From plant construction, underground mining to settlement dam builds, the company has learned to navigate the challenges of distance, unpredictability, and logistics. To stay ahead, GMS keeps healthy stock levels at its Cloncurry base. For everything else, they rely on smart supply partnerships.
One key relationship is with Mount Isa Mining Supplies, who do a weekly stock run to Cloncurry. Their rep, Emmalee O’Hara, has become a vital link in the chain. “Emmalee’s the next best thing to having a store in town,” says Turner.
“I send her a list of non-urgent items, and she’ll throw in extras she thinks we might need. It’s up to us if we buy them or not.”
It’s a practical solution to an impractical challenge; keeping critical parts flowing in some of Australia’s most isolated regions. Whether it’s a last-minute dash across the desert or a well-planned weekly run, partnerships like that between GMS and Mount Isa Mining Supplies keep the wheels turning in regional Australia. It’s not just about parts; it’s about trust, reliability, and backing each other when it counts. In the world of mining and industrial services, that’s the difference between a project stalling and a project finishing strong.
STOCKING UP
Diamantina Shire Council in Central West Queensland covers an area of over 94,000 square kilometres. Maintaining and building roadwork, both dirt and tar, is a major part of their core responsibilities. The works manager liaises with the engineers to set the schedule for the year, then coordinates with the work crews.
Josh Oehm is the workshop foreman at Diamantina Shire Council and part of his job is ensuring stock levels for the various work crews. The council’s remote locations must be factored into all supply decisions.
“Adequate amounts of tools, fasteners, fittings and bolts need to be on hand at all times,” he says. “It’s important because the work must continue smoothly and without interruption.”
Another Cloncurry-based business, Curry’s Diesel & Machinery, services the rural mining and commercial sector. The team covers everything from rebuilds to machinery hire to repairs.
“It takes a bit of foresight to ensure adequate stock levels to keep our business operating,” says Joe Robertson, workshop supervisor at Curry’s. “You need to plan ahead and allow for all eventualities. Time is money and any delay is costing our customers and ourselves.”
DELIVERY SERVICE
Diamantina Council is 500 kilometres from Mount Isa while Curry’s Diesel & Machinery is 115 kilometres away. Despite this, both businesses use Mount Isa Mining Supplies to supply tools, consumables and any specific items they require. The secret weapon is, once
again, Emmalee O’Hara. She loads up a van and hits the road to deliver whatever these businesses need.
“When we put in an order, we’re confident it will arrive during Emmalee’s weekly run,” says Robertson. “She will also have other items in the van for us to browse. Her instincts are usually right.”
Diamantina Council has the same service every fortnight. “The service they supply is excellent,” says Oehm. “When an item isn’t readily available, Emmalee will use her connections to find it for us.”
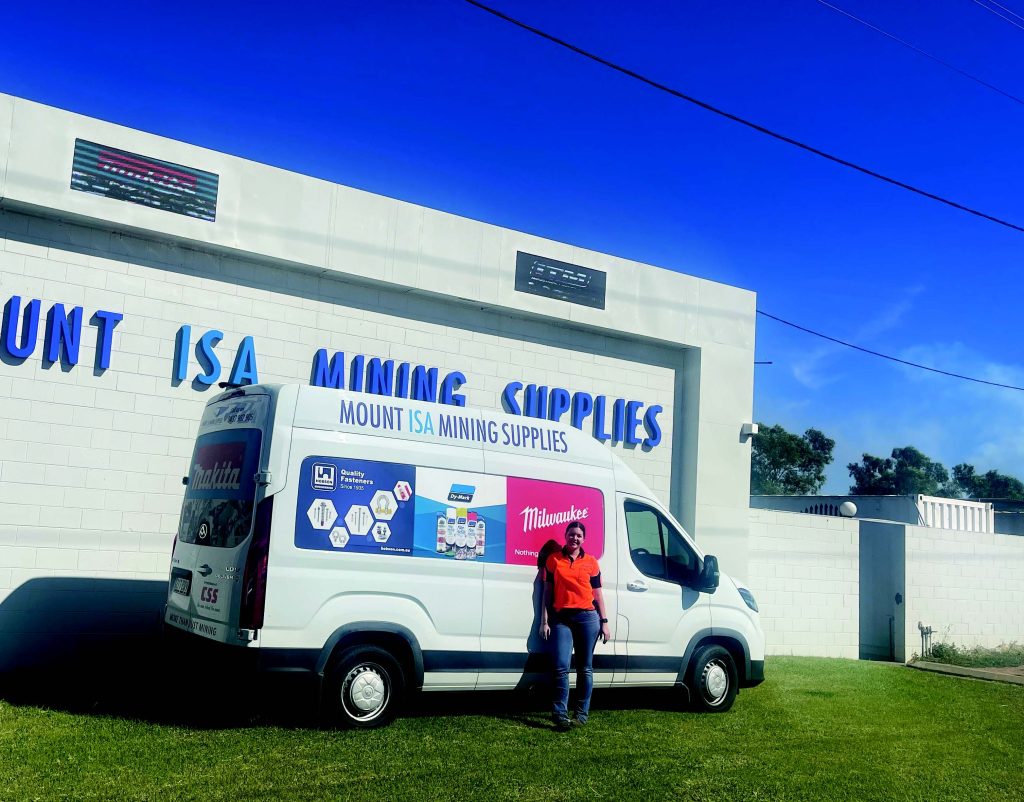
DEFEAT OF DISTANCE
Mount Isa Mining Supplies has overcome the problems of distance and delivery due to Brett Peterson’s firsthand experience prior to setting up the business.
“I spent 10 years underground handheld mining,” he says. “I saw all sorts of problems due to a lack of supply. When I started Mount Isa Mining Supplies in 2003, I knew it was imperative that customers be supplied with goods promptly.”
While still primarily a mining supply company, they deal with a wide range of businesses. “After all, anything used in the mines can be used anywhere else,” says Peterson. “And we’ll have it delivered on time.”