An accident during an off-road desert race stole Jamie Harrison’s ability to walk. But through perseverance and years of hard work, he has returned to once again conquer the event that so very nearly destroyed him. By Tracey Porter
The June long weekend will always hold special significance for fitter and offroad motorbike enthusiast Jamie Harrison. It was on that weekend in 2021 when a horrific high-speed accident almost cost the 54-year-old his life. And it was on that same weekend in 2024 that he conquered seemingly insurmountable physical and psychological challenges to boldly reclaim it.
Harrison, whose love affair with motorsport began when he was just eight, grew up in the country and spent all his spare time off-road racing.
Despite moving to Clontarf in Brisbane’s north later in his life, Harrison remained a thrill seeker at heart. For over a decade he was a regular race competitor in the extreme Finke Desert Race. Affectionately known as The Finke, the one-of-a-kind annual event sees hundreds of bikes and more than 150 buggies covering 452 kilometres of terrain from Alice Springs to the remote community of Finke and back over two days.
In 2021, Harrison was fiercely contesting The Finke, sitting in third position, when he saw an opportunity to chase down the competitor sitting second. Travelling at around 120 km/hr, Harrison then hit a hidden rock in a horror crash that saw him cartwheel into the air and slam into his own bike before hitting the ground.
Harrison suffered a life-changing spinal cord injury that resulted in permanent paralysis from the waist down. He spent five days in the ICU followed by 10 months in Adelaide Hospital where he experienced some of his darkest days. But then during this period, Harrison saw a glimmer of light when was visited by a friend who suggested he could return to The Finke—but in a buggy instead of on a bike.
Having set his sights on becoming the first paraplegic to enter the race, Harrison eventually approached good friend Darren Piper, a diesel fitter by trade who works as group merchandise manager at 4WD equipment group TJM.
Piper had raced with Harrison before his accident and was keen to offer the TJM workshop and its expertise in fitting and engineering to help Harrison solve a host of challenges both in the lead-up to and during the event itself.
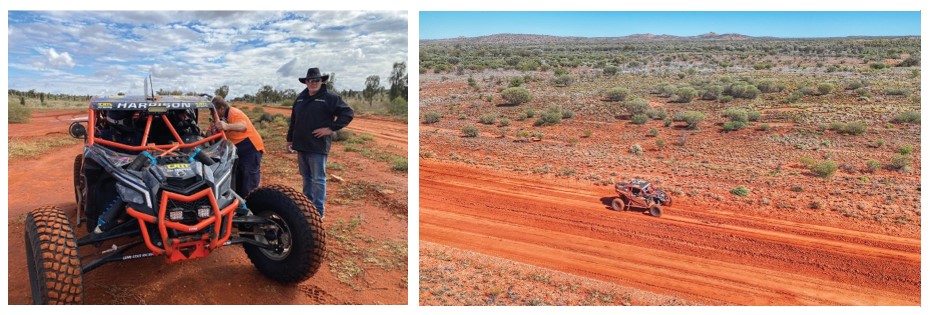
One of the toughest challenges was to overcome accessibility issues and help Harrison meet the race prerequisite of holding an offroad racing licence. “To be eligible, you must show the ability to get out of the car in under 10 seconds. For me to do this I first needed to modify the roll cage so I could get out in the required time. Once I got my licence, I then had to work out how I was going to drive the car with hand controls,” Harrison says.
“I also had to consider what my legs would do flopping around as we drive over some rugged terrain. The only available hand control kits for these buggies are very agricultural and mechanically clunky. I wanted something that gave me the chance to drive with some precision and accuracy, so I took what I learnt from what’s used in the road car industry for hand controls and modified them to be adapted to the race car.”
The buggy Harrison ended up racing can travel at around 145km/hr and is controlled via a specially adapted steering wheel with a throttle ring. A push bar brake rounds out the steering mechanism.
To give himself the best possible chance of a successful race return, Harrison also had to reacquaint himself with the tough desert conditions. This meant spending a couple of months in camp, enduring freezing nights and blistering hot days as part of his training.
He says it was here the TJM team came into their own, designing and building wheelchair-friendly gear—including custom-made showers and portable toilets—to allow him to successfully camp in a wheelchair in the outback. Harrison worked out for hours in the gym to prepare his body for the physical demands of the race as well as spent time behind the wheel to increase his driving stamina.
In June, he felt he was ready and lined up with some of the country’s toughest riders to contest the 48th running of the event. “I had a whole bunch of different emotions,” he recalls. “I was extremely nervous and scared because I didn’t want to get hurt again, and I just hoped my hands would hold up, but I was also excited to be back and doing what I love.
Despite numb and blistered hands and “a few scary moments” where he found himself airborne before going through the scrub sideways at 80km/hr, Harrison crossed the finish line with an impressive overall finishing time of four hours and 41 minutes—the first person with paraplegia to beat The Finke.
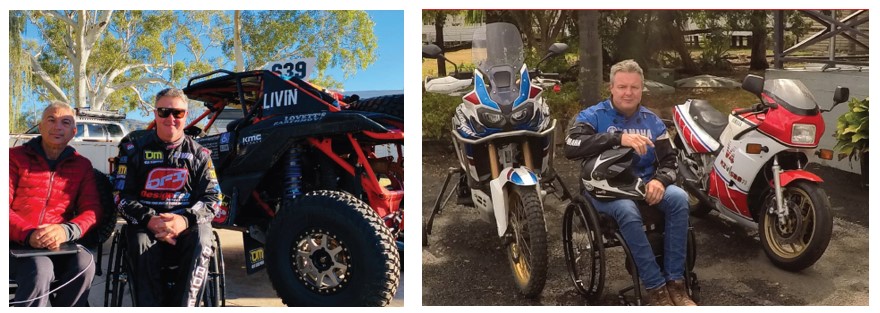
Harrison has now teamed up with not-for-profit mental health organisation LIVIN to help others who may be working through similar challenges. “In the beginning, if you’d told me that I’d be backing up and hooking up a big dual axel trailer, I’d be loading the trailer myself, I’d be putting it on, I’d have said, ‘Pig’s arse I will.’ But the fact that I can now tell people I’m doing this, I think gives them hope and helps them on their journey.”