The new Bridgewater Bridge is a Tasmanian first. It’s the largest transport infrastructure project in the state’s history, and will significantly strengthen Tasmania’s National Highway.
Once complete, the $786 million bridge will span the Derwent River with around 22,000 vehicles expected to cross the 1km-long bridge each day.
The fixed structure bridge will provide 16.2 metre high clearance over the navigation channel, and feature four traffic lanes and a shared bicycle and pedestrian path.
With the Australian and Tasmanian Governments committed to having the new bridge open to traffic by the end of 2024 and completed in mid 2025, it’s a major project on an ambitious time line. But some of Tasmania’s leading construction and supply companies are drawing on their longstanding relationships and local know-how to help meet the challenge.
LaTrobe-based BridgePro Engineering is assisting construction contractor McConnell Dowell, and it’s a project that BridgePro founder and managing director Aaron Brimfield says serves up some interesting challenges.
“It’s the largest project of its kind ever in Tasmania, and a once-in-a-lifetime opportunity for us,” he says. “We’re working on a reasonably compressed timeline, and the bridge needs 90-metre-long piles which will be some of the longest in the world. The project also requires the construction of a temporary bridge to enable the movement of materials and equipment—such as large cranes and construction equipment—across the River Derwent, and BridgePro is hard at work helping to construct it.
“Twelve barges have been brought in to form the southern section of the bridge, which will be linked to a steel bridge that will sit on 72 piles,” Brimfield explains. “So just constructing the temporary bridge is a relatively large project in itself.”
But that’s only the beginning. The construction process for the main bridge began in 2022 with land reclamation on the southern side of the river, and the construction of a temporary working platform on the northern side. An onsite precast facility was built to produce the more than 1000 concrete bridge segments that will be required. Major earthworks were also required on the southern foreshore, and BridgePro is working on the form reinforcement for the bridge’s huge 42 piers.
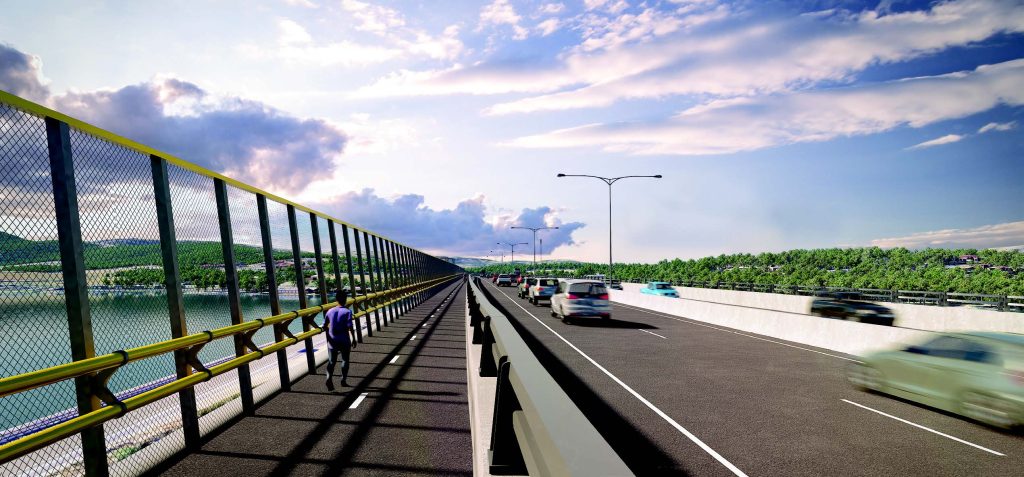
“Each pier is 150 cubic metres, and they all require double reinforcing cages for extra strength because the bridge is so long,” says Brimfield. “We’re fabricating the cages, but they’re too large to be produced on a cage-making machine.”
So BridgePro is adding around 30 new local workers to its team.
“We’re proud to be doing a lot of the prefabrication work in our facility in LaTrobe that’s more than 200km north of the bridge site. So the project is really spreading economic benefits across Tasmania.”
Tasmanian born, bred and built BridgePro’s expanding team isn’t the only beneficiary of the project. It will support around 1000 direct and indirect jobs and create more than 250 new jobs. Tasmania-based suppliers, such as Rapid Supply and BuildTech Supplies, are also being engaged wherever possible to keep the project’s wider economic impact focused on Tasmanian businesses.
CSS member Rapid Supply is a proudly Tasmanian owned and operated specialised construction supply company. Jamie Kunta, civil & construction technical representative at Rapid Supply, says the company is supplying a broad range of products to the project, including fasteners, rigging, lifting, grouts, epoxies and personal protection equipment.
“We’ve had a long relationship with BridgePro and they have been a big support to us over many years,” he explains. “Due to that relationship, we’re able to work very closely with them and keep items they need in stock on the island, so they are available immediately. We’ve also had opportunities to supply McConnell Dowell with other materials for the project, which is part of the flow-on effect a project of this size has had for us and other Tasmanian businesses.”
BuildTech Supplies is another one of those businesses. It is also a proud Tasmanian company and a CSS member and has had a longstanding relationship with BridgePro.
“We’re supplying a range of product lines, supported by our technical knowledge to assist all the contractors on site. Furthermore, we have a representative onsite daily working through issues with engineers and making sure they get the right advice and products,” says Greg Ellingworth, Technical Sales Representative at BuildTech Supplies.
“This project is a very, very big deal for Build Tech, but it’s not just us. There are a number of Tasmanian companies on the ground helping with this project. It’s all about teamwork and using the relationships and trust we have with each other to add value and get results. We are 100 per cent invested in our clients. We know that if they succeed, we succeed, and the project succeeds.”